无线充电pcb板DIY
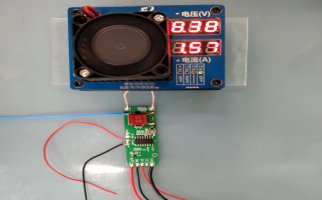
在智能手机与物联网设备日益普及的今天,无线充电技术正悄然改变人们的生活方式。一块巴掌大小的电路板,如何通过精密的线圈布局与材料选择,实现隔空传递能量?本文将从设计原理到实践操作,揭开无线充电PCB板DIY的神秘面纱。
能量传递的核心:电磁感应与电路设计
无线充电的本质是电磁感应原理,发射端线圈通过交流电产生磁场,接收端线圈感应磁场后转换为电能。核心电路需包含发射模块(如XKT510)与接收模块(如T3168),搭配谐振电容实现能量高效传输。发射端电路还需集成升压模块,将电池电压提升至工作所需范围,并通过跳帽设计实现输出电压灵活切换,例如兼容5V手机充电或更高功率设备。
材料选择:耐高温与柔韧性的平衡术
PCB基材如同电路的“骨骼”,直接影响能量转化效率与耐用性。聚酰亚胺(PI)材料因具备耐高温(可承受150℃以上)、抗化学腐蚀和柔韧性,成为无线充电PCB的首选。这种材料能抵御线圈工作时产生的局部温升,避免电路板变形或性能衰减,如同为电路穿上一层“耐热防护服”。铜箔厚度则需控制在18-35μm之间,过薄会导致电流承载能力不足,过厚则会增加涡流损耗——这类似于水管太细容易爆裂,太粗则水流阻力反而增大。
制作流程:从设计图到实体板的四步进阶
原理图绘制与仿真验证
使用Altium Designer等EDA工具绘制电路图,重点优化线圈直径、匝数与间距参数。通过仿真软件模拟磁场分布,规避“能量空洞”(即充电区域信号弱的位置),这相当于在虚拟考场中提前演练,避免实物测试时反复修改。
布局优化的三重法则
电磁兼容性优先:将高频振荡电路远离敏感元件,采用铺地屏蔽技术降低干扰,如同在城市规划中设置绿化带隔离工业区与住宅区
热管理策略:功率器件周围预留散热孔,高温区域避免布置电解电容,可采用热敏电阻实时监测温度
安全冗余设计:加入过压保护芯片与保险丝,防止线圈短路时损坏设备
打样测试的双阶段策略
首次打板建议分模块验证:先制作纯线圈结构板测试磁场强度,再完成完整电路板测试充放电效率。第二次打板时可根据测试数据微调参数,例如将线圈间距从1.2mm调整为0.8mm以增强耦合效率。
组装调试的“三频段”检测法
使用示波器观察谐振频率是否稳定在100-200kHz范围(相当于无线充电的“语音通话频段”);用热成像仪检测工作时是否有局部过热点(超过85℃需重新布局);最后通过实际设备测试充电效率,达标线通常为60%-75%。
常见难点与优化技巧
DIY过程中最易出现的问题是电磁干扰(EMI)导致充电不稳定。可通过以下方式改善:
在整流电路输出端增加π型滤波器,如同在高速公路设置减速带,平缓电流波动
采用分层绕线法替代平面螺旋线圈,将发射线圈分为上下两层交叉布线,既能缩小体积又可提升磁场均匀性
当接收端偏移时,可在PCB边缘添加铁氧体磁片引导磁场走向,类似用导流板控制水流方向
从实验室到生活场景的适配升级
完成基础功能的PCB板后,可通过添加智能控制模块实现场景化应用。例如集成红外传感器,当检测到手机放置时自动激活充电;或连接Wi-Fi模块实现充电状态远程监控。这些改进如同给传统机械表添加陀飞轮装置,在基础功能上叠加智能化层次。
通过层层拆解不难发现,无线充电PCB板的DIY过程恰似一场精密的空间艺术创作。从纳米级的铜箔厚度控制到厘米级的线圈布局,每个细节都在演绎电磁世界的微观美学。当第一盏通过自制电路板点亮的LED灯闪烁时,那些伏案调试的夜晚终将化作科技与创意碰撞的火花。